Stainless Steel Supplier
303, 304, 316 & 410
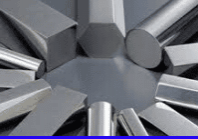

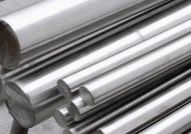
The One Stop Metal and Plastic Shop
303 Stainless Steel
Grade 303 stainless steel is the most suitable for machining among the austenitic stainless steels and is the free-machining variant of Grade 304. It is primarily used when extensive machining is required during production. The addition of sulphur and phosphorus, which enhance its machining and anti-galling properties, reduces its corrosion resistance compared to Grade 304. While it offers good resistance in mildly corrosive environments, it is significantly lower than that of Grade 304.
The presence of sulfur also negatively impacts the weldability and formability of Grade 303, making it unsuitable for applications involving sharp bends.
Grade 303 exhibits good oxidation resistance at temperatures up to 760°C in intermittent service and up to 870°C in continuous service. However, due to the risk of carbide precipitation, it is not recommended for continuous use between 425-860°C. It is also prone to sensitization since it typically does not have a low carbon content.
Grade 303 is not ideal for marine environments, where it is susceptible to pitting corrosion. The sulphides in Grade 303 are mainly oriented along the rolling direction, which further reduces its corrosion resistance in cross-sections.
Despite the slight reduction in toughness caused by the sulphur, Grade 303 remains tough and, like other austenitic stainless steels, is prone to stress corrosion cracking in chloride-rich environments above 60°C.
304 Stainless Steel
Grade 304 stainless steel is the most widely used and versatile of all stainless steel grades. It is available in more forms, finishes, and applications than any other type.
With its balanced austenitic structure, Grade 304 can be deep-drawn to an impressive extent without requiring intermediate annealing. It also has excellent oxidation resistance, withstanding intermittent exposure to temperatures up to 870°C and continuous exposure up to 925°C. However, continuous use in the temperature range of 425-860°C is not recommended if resistance to aqueous corrosion is important.
Grade 304 performs well in a wide variety of atmospheric conditions and corrosive environments, though it is vulnerable to crevice corrosion and pitting in warm chloride conditions. Stress corrosion cracking can also occur at temperatures above 60°C.
For maximum corrosion resistance, heavy-welded sections may require post-weld annealing, though this is unnecessary for thin sections. The steel has excellent forming and welding properties using all standard fusion techniques, with or without filler metals.
In addition to its versatility, Grade 304 is known for its overall toughness and excellent low-temperature properties, which respond well to hardening through cold working. It is also easy to fabricate and clean, making it a popular choice in many applications.
316 Stainless Steel
After Grade 304, Grade 316 is the second most common austenitic stainless steel. It offers excellent toughness, even at extremely low cryogenic temperatures.
Grade 316 is the standard molybdenum-bearing stainless steel, known for its superior corrosion resistance in various atmospheric conditions and corrosive environments. It has significantly better resistance to pitting and crevice corrosion than Grade 304, but in warm chloride environments, these issues, along with stress corrosion cracking above 60°C, can still occur.
Like Grade 304, 316 stainless steel has excellent forming and welding properties, using standard fusion methods with or without filler metals. The post-weld requirements for heavy welded sections and thin sections are the same as for 304. Its oxidation resistance is also comparable to that of Grade 304.
Grade 316 is widely used in the handling of certain food and pharmaceutical products, where minimising metallic contamination is critical. It is often referred to as "Marine Grade" stainless steel due to its increased resistance to chloride and saltwater corrosion. However, it is not fully resistant to warm seawater. Surface corrosion, typically seen as brown staining, can occur under these conditions.
410 Stainless Steel
Grade 410 stainless steel is a fundamental martensitic stainless steel known for its ability to achieve high mechanical strength through heat treatment. It offers a good balance of toughness, ductility, and resistance to corrosion and scaling at temperatures up to 649°C. These characteristics make it an excellent choice for applications requiring both strength and durability in challenging conditions.
Its high strength and good corrosion resistance in mild environments such as steam, mild chemical settings, and atmospheric conditions make it ideal for highly stressed components. Due to its mechanical properties, Grade 410 is commonly used in a range of industries. In automotive applications, it is often found in vehicle exhaust systems, manifolds, and other high-temperature engine components. Its durability and resistance to wear also make it suitable for medical instruments and devices, where strength and hygiene are essential.
Additionally, 410 stainless steel is frequently employed in petrochemical industries due to its ability to withstand the corrosive conditions present in these environments. Though its corrosion resistance is lower compared to austenitic stainless steels like 304 or 316, it performs well in less aggressive environments and is valued for its high strength and cost-effectiveness.
It can be hardened and tempered to achieve higher wear resistance, further expanding its range of applications in industries that demand both mechanical strength and corrosion resistance at elevated temperatures.
The chromium content in stainless steel creates a passive layer of chromium oxide that resists corrosion and rust. However, under certain conditions, even stainless steel can rust. Maintaining a clean surface and avoiding prolonged contact with harsh chemicals can help prevent rust.
Yes, Colt Materials have a cutting service so you can order custom measurements for all metals and waste less material! Enquire about our cutting service today.
Stainless steel is famous for its resistance to rust, but it's not entirely rust-proof. The key to stainless steel's success is the chromium content (minimum 10.5%). This chromium reacts with oxygen to form a thin, invisible layer of chromium oxide on the surface. This layer acts as a barrier, significantly protecting the steel underneath from rust and corrosion. While the chromium oxide layer is excellent protection, under certain circumstances, even stainless steel can rust.
Stainless steel's enduring popularity stems from its exceptional combination of properties, making it a champion material in numerous applications. Food and beverage equipment, architectural applications, chemical processing equipment, medical and dental equipment, automotive parts, hardware, and more...